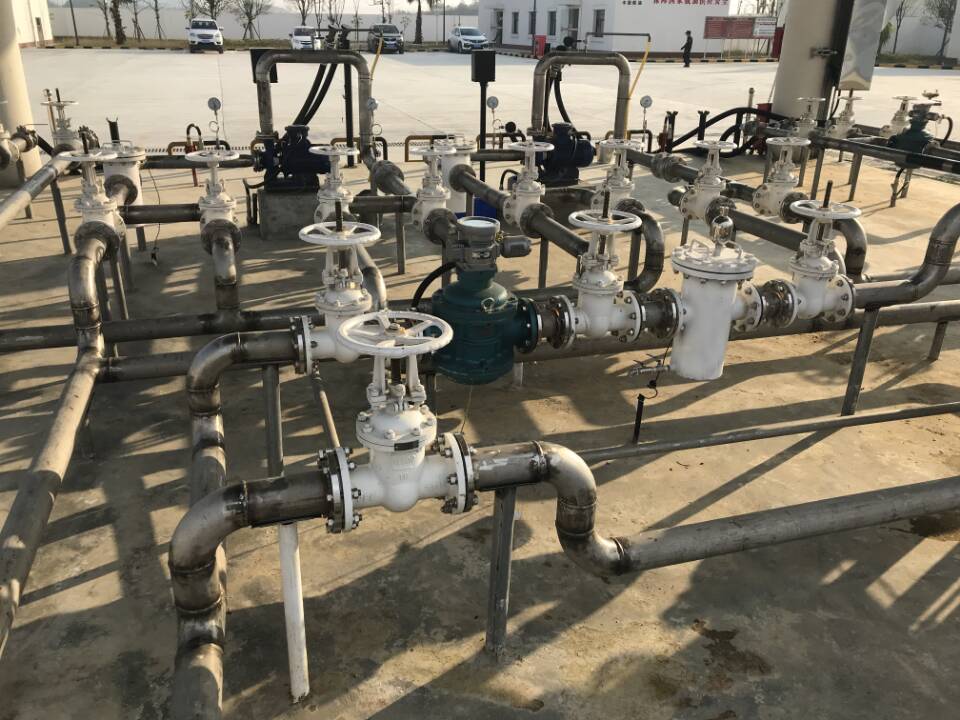
Installation of Oval gear flowmeter
1. Users should clean the pipeline before
installation the oval gear flowmeter.
-
If the liquid contains solid particles, a
filter must be installed in the upstream of the pipe;
-
If the gas is contained in the fluids, an
exhaust gas device should be installed.
-
The new pipeline should be cleaned before
operation, and then it should be subsequently flushed with a solid flow to
remove residual welding scales.
-
The stop valves in front and after of the flowmeter
should be closed to allow liquid to flow from the bypass tube;
-
if there is no bypass tube, the flow meter
should be equipped with a short tube instead.
2.The oval flowmeter has no certain
requirements for the straight pipe sections before and after the oil flow
sensor. It can be installed horizontally or vertically. When installing, the oval
gear rotation axis of the flowmeter should be parallel to the ground.
3.The flow direction should be consistent
with the direction indicated on the flow metering housing. Generally, it can
only be measured in one direction. If necessary, the reverse valve is installed
downstream to avoid damage the flowmeter
4. Usually
after the liquid sweep, there is still air in the pipeline, with the pressure
running, the air flows through the flow sensor with a higher tassel, the active
measuring components may run too fast, damage the shaft and bearings of the
flow sensor. Therefore, the flow should be slowly increased at the beginning to
make the air gradually escape.
How to use oval gear flowmeter ?
1. Check the filter
The new pipe line startup filter network is most easily broken. After the test run, it is necessary to check whether the pipe line network is in good condition. At the same time, when the filter is clean and free of dirt, users should record normal flow and pressure loss for the future reference.
2.Measuring high viscosity liquid
Oval gear flow meters are suitable to measure high viscosity liquids, users need to generally heat the fluids to flow when start to use the flow meter again. When the flow meter is stop working, its internal fluids is cooled and thickened. When it is working again, cooled fluids must be heated before it flows through the flow sensor. The flow sensor measuring component will be damaged by the thick cold flow.
3. Avoid sharp flow changes
A sharp flow change produces a large additional force that damages the gear rotor which could easily damage the flow meter.
4. Bypass pipe switching
When the liquid flow is transferred from the bypass pipe to the meter, users need to open and close the bypass slowly, especially on the high temperature and high pressure pipeline. When it is activated, open the inflow side valve, then slowly open the valve on the outlet side, observe the running condition of the flow meter, and finally close the bypass valve. The optimum flow rate should be controlled at (70~80) % of the maximum flow to ensure the service life of the instrument.
5. The operation flow
The min flow should not be too small, the operation flow should be operation within the value which indicated on the flow meter name plate, and otherwise the oval flow meter could have poor accuracy.
6. The medium temperature
The medium temperature should not be too high. It should be within the temperature indicating one the name plate, otherwise it could have the possibility of jamming the gear
7. Regularly check the gear condition.
After long-term use of the oval gear flowmeter, the internal gears will be corroded and worn, which will affect the measurement accuracy. Therefore, always pay attention to observation, and regularly remove it for inspection and re-calibration.